How is a football made?
Discover how a football is made, from material selection and panel cutting to stitching, lacing, and quality inspection for game-ready performance.
Football, or soccer as it is known in a few cultures, is the most loved game all over the world, with millions of fans, players, and supporters. The football itself is at the center of the game: a product that has been psychologically and physically considered to develop, as it is essential for the sport. In this article, we will discuss football assembling, from design to the finished product, focusing on the materials, manufacturing processes, and technology involved. And if you are looking for high-quality football shirts? Check out Football Shirts for the latest designs and top-notch jerseys for every fan!
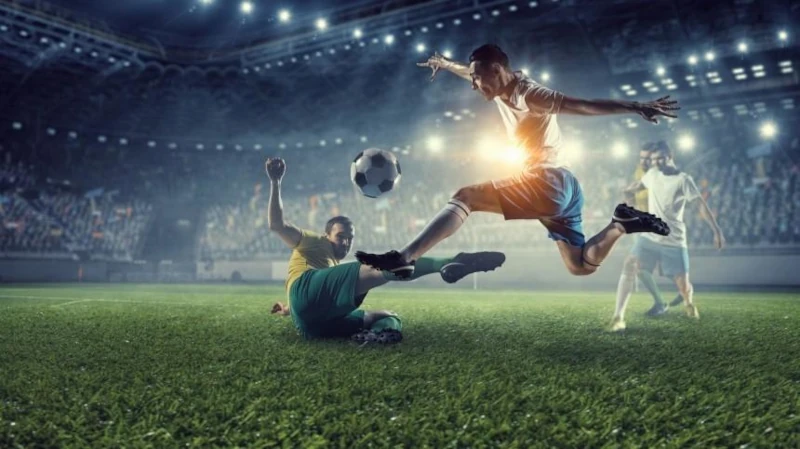
The Art and Craft of Making a Football
Step 1: Select the Material
Earlier, the leather-wrapped football was much in vogue, but at the present time, synthesized materials are used mainly because these enhance the performance of the football, give it durability, and make it rain and shine-proof.
Outer Cover: The outer cover of the ball is made from synthetic leather or Polyurethane. These materials are preferred because they are
- Durable
- Water Resistant
- Offer better control and grip.
Bladder: In between the football ball is a bladder that holds air and enables the ball to maintain its shape and bounce. This organ is usually made of latex or rubber and is an important element in maintaining the football's firmness and functional properties, including its responsiveness and control when kicked.
Stitching Materials: The football is stitched up using tough threads, which usually are nylon or polyester, so that the football remains intact, as it suffers the wear and tear of kicks, headers, or tackles.
Step 2: Designing the Football
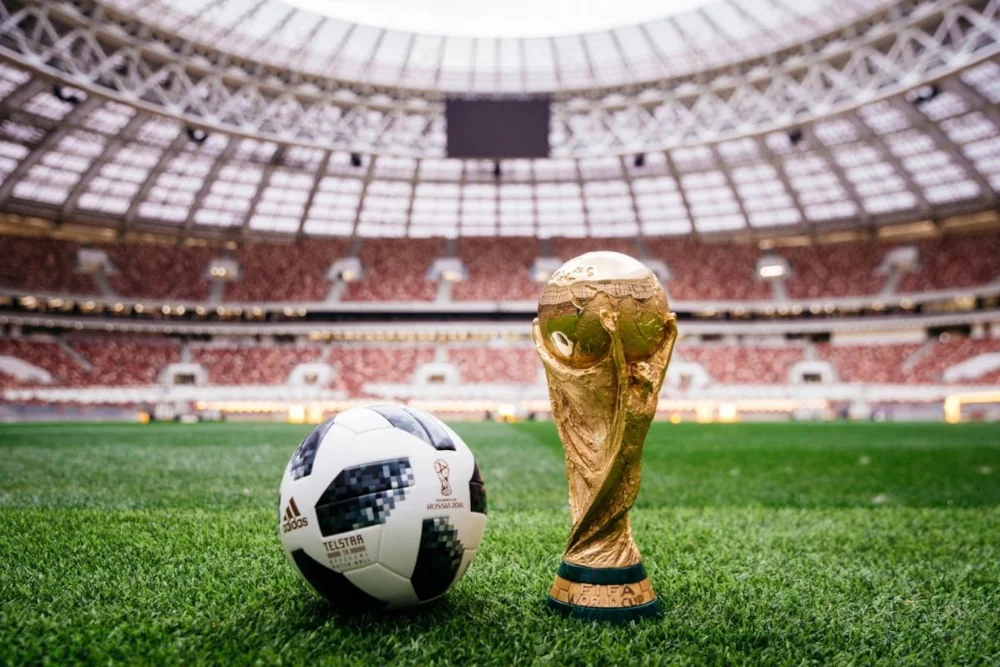
In the earlier period, when such standards were not set for the footballs, they were manufactured of different shapes, sizes, and designs. The footballs in those days could be spherical, ovoid, or oval along their ends. Currently, the standard for a football is that it should be round and symmetrical and should have certain specific dimensions.
- Panel Design: The most popular football design is a design of 32 panels made up of a combination of hexagons and pentagons. It was famously used in the Adidas Tango España, in use during the 1982 FIFA World Cup. These days, however, footballs can also come with fewer panels, and in some designs, only 6 to 12 panels can be used. The optimization of the shape and arrangement enables aerodynamics and performance.
- Printing and Branding: After the design of the ball has been finalized, they will determine what branding and graphic aspects to print on the surface of the ball.
Step 3: Cutting the Panels
Once the materials and design have been fixed, the process cuts the panels forming the football. The panels usually have synthetic leather or polyurethane sheets, cut with the aid of precision cutting machines.
They should most commonly be cut into hexagonal or pentagonal shapes, with each mold designed to fit together in such a way that they form a spherical model.
Each panel is cut to a specific size so the football can meet the government's specifications, such as weight, circumference, and bounce.
Step 4: Stitching the Panels together
After all the parts are ready, the football panels need to be properly joined with stitches. Building secure connections between individual parts creates strong and reliable football panels.
- Production machines join the panels together to make multiple footballs at once. Fully automated machines handle the panel placement at exact positions as they attach the panels with robust thread.
- Top-quality football balls used by professionals include hand stitching as their primary method of joining panels. Hand stitching takes more time.
- The football design features carefully placed stitches, which help keep the ball-shaped while avoiding defective seams that affect flight.
Step 5: Inserting the Bladder
The bladder is the part inside the ball that actually holds the air and gives the football its bounce as well as shape. The bladder is made of either rubber or latex materials known for their elastic properties.
- Insertion of Bladder: After the stitching of the panels of the ball is done, then the bladder is to be inserted into the ball. This is the most important step because if the bladder is not inserted properly or inflated properly, it will not work on the playground.
- Bladder Inflation: Upon inserting the bladder within the ball, air is then pumped through it to achieve the desired air pressure. This pressure generally varies between 8.5 and 15.6 psi, depending on the purpose for which the ball is put to use.
Step 6: Sealing and Final Stitching
The heat-sealing of upper-class footballs closes the panels and eliminates the need for stitching. The process bonds panels with heat and pressure for a smooth finish.
Professional gate footballs or international competition-grade footballs typically prefer heat-sealing as opposed to traditional stitching. This process gives an even and smooth surface, and it is also done to prevent the ball from soaking up water, which can affect its performance. For balls that are not heat-sealed, the final stitching is done to close the opening.
Step 7: Quality Assurance and Trials
Once built entirely, the ball goes through essential tests to show that it meets production requirements for quality and protection. These comprise:
- Rebound and Contour assessment
- Mass and perimeter evaluation
- Strength and environmental resilience
Step 8: Packing and Division
The football is divided when its packing is done. The balls are wrapped and packaged in order to minimize damage while being carried away and then sent to retailers or teams for their eventual use.
The Future of Making a Football
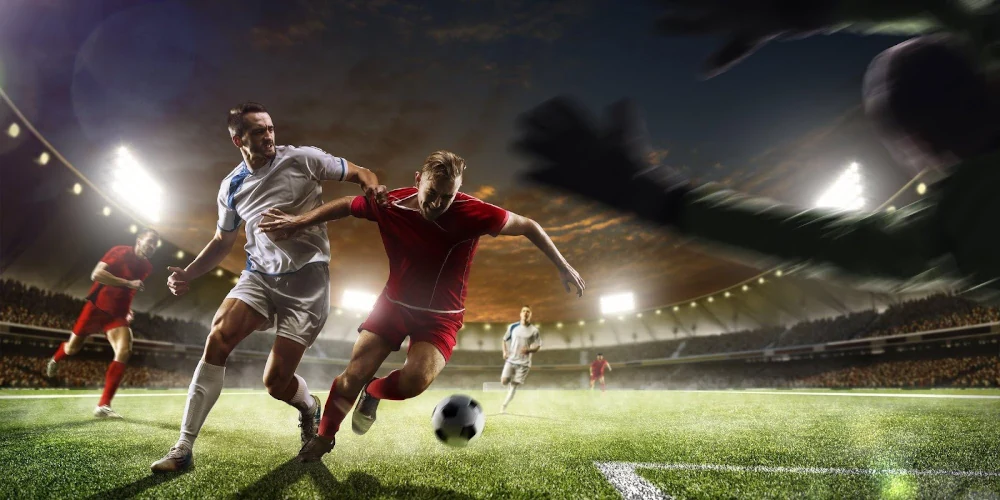
In addition, football manufacturing will embark upon substantive transformations on account of technology, materials science, and customer preferences. As the growth of the sport persists, along with its innovations, the balls in use will be modified to cater to the application of the players, followers, and the environment.
Top Football Manufacturing Companies
Adidas
Adidas is one of the most widely known sports brands. For years, the company has been an authority in the football manufacturing world, making footballs for a host of major tournaments like the FIFA World Cup and UEFA Champions League.
Famous Products: The Adidas Tango, the Brazuca (2014 FIFA World Cup ball), and the Adidas Telstar (2018 FIFA World Cup ball).
Nike
Nike is another popular worldwide brand in sportswear and equipment. The company will also manufacture footballs being used in different leagues and competitions around the world.
Top-selling products: The main balls include the Nike Ordem series, Nike Merlin (used in the English Premier League), and the Nike Flight (used in the UEFA competitions).
Puma
Puma is a reputed sportswear brand based in Germany that makes some high-quality football. This has led to collaborations with several leagues and clubs to supply their balls for competitions or training sessions.
Famous Products: Puma evoPOWER and Puma Future Grip footballs.
Ronaldo is considered to be the one of the best football players in the world. His fans throughout the world love to wear ronaldo football shirts.
Conclusion
The making of a football implies a chain of several operations of craftsmanship followed by technology. From material selection to final tests, each operation has an important role to play in the construction of that ball to perform on the pitch. Be it a professional match or just for pleasure, football has witnessed detailed and precise processing to become the perfect instrument for the beautiful game. With advances made in materials, designs, and manufacturing techniques, modern footballs give unmatched quality and performance to the players wherever in the world.