A well-organized warehouse is the backbone of any efficient shipping and handling operation. When products are well organized, employees can locate them in a snap, fill orders on schedule, and avoid costly errors. With the time-strapped market of today, customers expect merchandise to be shipped out immediately, and a disorganized warehouse can lead to unnecessary delays, lost products, and excessive stress on employees.
In addition to speed, an optimized warehouse is safer, more space-efficient, and overall more productive. Organized companies not only optimize their operations but also gain a competitive edge since they fulfill customer requirements with precision and reliability. Whether your business is a small online shop or a large distribution center, having a well-organized warehouse is crucial for long-term success.
Below are eight reasons why an organized warehouse is essential for rapid shipping and seamless order processing.
Optimized Space Utilization for Maximum Efficiency
Warehouses with congested aisles and inefficient storage designs squander valuable space and hinder operations. A strategic organization optimizes the utilization of every square foot of storage, allowing inventory to be accessed and retrieved more efficiently.
Installation of vertical storage units, stock location assignments, and proper grouping improves the efficiency of the workflow. A warehouse specifically engineered with modular construction systems will also maximize space usage by providing flexible storage and expandable storage areas that can facilitate the company to manage changing needs for stock space more effectively. Space optimization enables companies to move more products without expanding the area needed on the floor, reducing costs and overall improving shipping and handling efficiency.
Faster Order Processing and Fulfillment
An organized warehouse enables workers to easily locate products, reducing the time taken in picking, packing, and shipping orders. When inventory is stocked in a structured way and tagged clearly, and also with specified zones, workers are able to navigate the space better, without further delays. This is particularly true for firms with large order volumes where minute inefficiencies in the system can together result in huge delays.
Proper shelving, automated inventory management, and streamlined workflows enable each order to pass through the fulfillment process without interruptions. As a result, customers' shipments arrive on time, leading to greater satisfaction and repeat business. Faster order processing also reduces labor costs and improves overall warehouse efficiency.
Reduction in Picking and Packing Errors
Order fulfillment mistakes can be a nightmare—leading to returns, angry customers, and even damage to your brand reputation. A disorganized warehouse makes it worse, contributing to the chances of picking the wrong item or forgetting something in a shipment.
However, a little bit of organization can go a long way. Simple strategies, such as barcode scanning, color-coded shelves, and inventory management software, can significantly reduce errors. If employees have an organized workspace to work from, they're less likely to grab the wrong item or skip essential packing steps.
Furthermore, with packing stations standardized and having checklists, this ensures each order is of quality before shipping out the door. That means fewer mistakes, happy customers, and a smoother operation overall.
Enhanced Employee Productivity and Safety
Warehouse organization isn't all about efficiency—it's also about safety. Mess can lead to accidents like trips, falls, or even equipment crashes, putting your employees at risk and slowing everything down. But with clear pathways, designated storage areas, and proper safety protocols in place, you create a safer, more efficient work environment.
A well-planned storage also has less confusion. When staff know exactly where all the parts go and the way the task must flow, they can accomplish tasks more swiftly with more confidence. Less pressure, fewer mistakes, and more streamlined operation all the way around. In the long run, a well-planned warehouse does more than improve productivity—it equates to an enhanced workplace.
Better Inventory Management and Stock Accuracy
If your warehouse is disorganized, inventory management can be a disaster. You might overstock, be out of critical products, or even lose products along the way. But with a system in place and real-time tracking, you can keep your stock under control and make sure that you always have the products you need to ship out orders on time.
With technology like RFID, barcode scanners, and warehouse management software (WMS), the guessing is removed and the role of human error minimized. With an open visibility of your inventory levels, you can more easily predict demand, restock properly, and avoid expensive shortages or overstocking. And with accurate inventory, you ship faster—no more searching for missing pieces and delaying orders.
Faster Receiving and Restocking of Inventory
An organized warehouse is not only about shipping orders—it's also important for efficiently receiving and restocking stock. When shipments come in, having a system in place ensures that they get checked, documented, and put away in the proper places efficiently. Without a plan, incoming stock can accumulate, causing restocking and order processing delays.
A well-designed process for receiving, inspecting, and staging products keeps inventory in continuous motion, so products are always available when needed. This not only minimizes downtime, but also keeps storage areas uncluttered with masses of unprocessed inventory, keeping operations running smoothly.
Cost Savings on Labor and Storage Expenses
If your warehouse operations are disorganized, you're probably paying for more labor than you need to. Time spent searching for things, fixing mistakes, or keeping a messy stockroom adds up fast. But with a rational layout, smart storage space, and a bit of automation, you can reduce the time and effort it takes to do each thing.
And, instead of spending money on increased storage space, you can get the most out of what you already have—sparing the expense of expansion. Reducing operations saves you money and keeps productivity high. And the icing on the cake? Those savings can be funneled right back into business operations, be it to enhance logistics, speed up deliveries, or enhance customer service.
Improved Customer Satisfaction and Brand Reputation
Customers want their orders fast and right—no one likes to wait forever or get the wrong item. That's why a well-planned warehouse is what makes all the difference. If it takes forever to ship, items get lost, or the wrong items are sent, then negative reviews and lost business are the outcomes.
But when a warehouse operates at peak level—with streamlined storage, speedy order fulfillment, and few errors—customers receive precisely what they ordered, right on schedule. Satisfied customers are more likely to return and recommend your company, enhancing your brand reputation. In today's competitive marketplace, with expectations higher than ever, keeping your warehouse at its best is the way to win customer confidence and establish long-term loyalty.
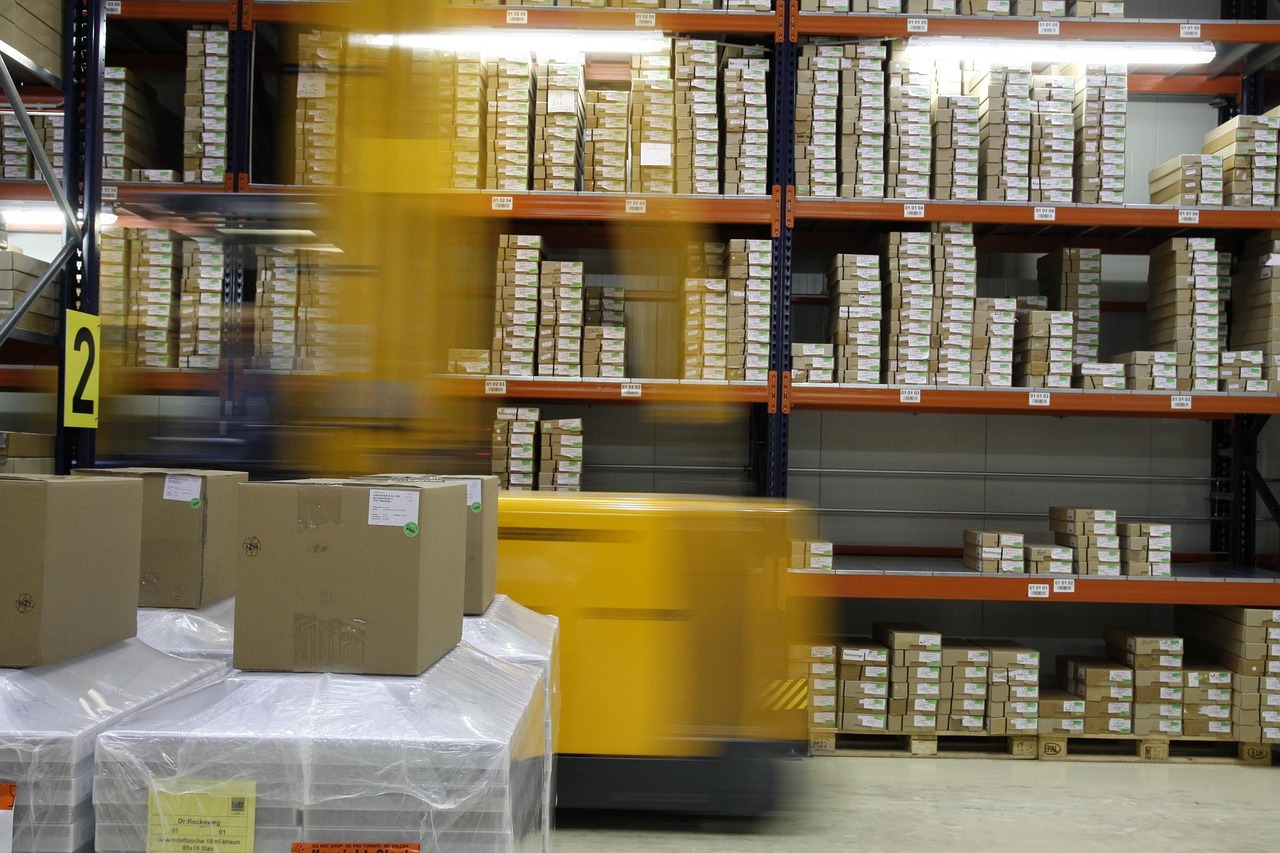
Maintaining a tidy warehouse is not just a matter of looking neat—it's the key to rapid shipping, fewer mistakes, and happier clients. When goods are where they belong, shipments go out cleanly, employees get more done, and you avoid the frustration of missing inventory or late shipments. And it even saves you money by cutting time lost and storage costs. If customers are looking for lightning-fast delivery, having an organized warehouse is a competitive edge. Hence, if you want to achieve greater productivity and maintain customer loyalty, investing in better organization is one of the best options available.